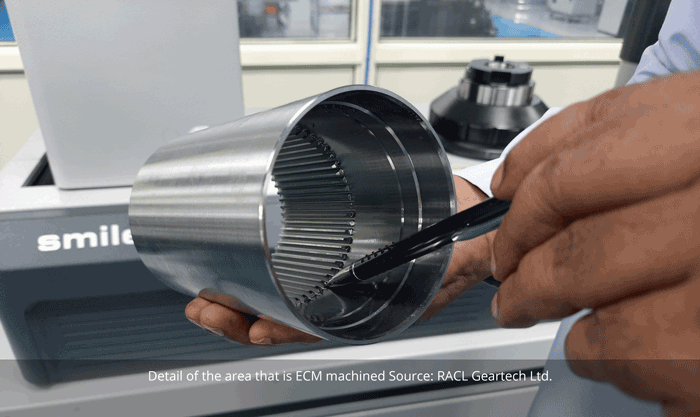
ECM (Electrochemical Machining) solved RACL Geartech key project deburring issue.
Mr. Gursharan Singh, Chairman and Managing Director at RACL Geartech Ltd. talks about adding Electrochemical Deburring to his gear manufacturing capabilities.
Extrude Hone is honored to share with you a testimonial provided by Mr. Gursharan Singh from RACL Geartech Ltd. In India, the company was established in the year 1989. Company is producing Gears, Shafts, sub-assemblies & Precision machined components for diverse application in Motorcycles & Scooters, 3 and 4-wheeled vehicles, passenger cars, agricultural machinery, tractors, off road vehicles, ATV, Light and Heavy-Duty Commercial vehicles. The parts & aggregates are being used for Transmission, Engine Timing, Torque Limitation & critical safety applications for Chassis & Braking systems.
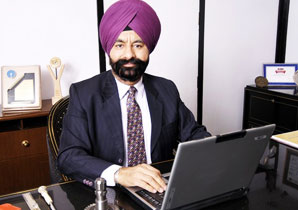
As Mr. Gursharan Singh says:
Predominantly our company is into the business of manufacturing gears, shafts & parts for automotive applications. You know, we are in this business for over 30 years and burrs presence has always remained a big challenge in manufacturing of the gears. By the way, not only RACL, but any other gear manufacturers will also confirm, that, historically burrs have always remained the problem. Unfortunately, it’s little tricky situation that on one side, burrs are the problem and on the other side no customer wants to pay anything for burr removal. So, it is a complex situation. At least in Indian context, gear manufacturers are little hesitant for investing in high -end technology for deburring applications.
Incidentally, our company started a new business relationship with ZF, Germany, for some critical applications for Ring Gears for Chassis applications, where we really faced a peculiar problem of burrs in Internal teeth, which was not accessible for any mechanical or manual deburring. The burr removal was a big problem by any conventional method. So, this is where ECM (Electrochemical Machining or Electrochemical deburring) came in. I had some vague idea, that Electrochemical deburring is a process, which people are using extensively in high-end industries like aerospace. Eventually, we started hunting for this technology. You know, Bangalore in India is a place where there is a lot of aerospace industry. Incidentally, I know one of the manufacturers who does aerospace business. Probably he was getting some aerospace parts processed by Extrude Hone India. He guided me & recommended that “okay, if you have this complex product, go to Extrude Hone India & they will support you”. Although. he cautioned that process is very, very expensive, yet I still decided to get more details as we were stuck badly on the particular part. Nevertheless, I went to Extrude Hone India, and then eventually things moved very, very fast.
I personally, spoke with the Managing Director Mr. Debnath Goswami. He was very prompt and agreed for trying out few parts to show how this deburring process looks like. We issued a preliminary order to produce 50- 60 parts, and we found our problem gets resolved by this process. Since, I had plans to visit Germany for a business trip, I took the opportunity to visit Extrude Hone Germany as well. To be very honest, I was highly impressed by the enthusiasm shown by your Managing Director Mr. Wolfrat & detailed technical explanation by Extrude Hone German team experts. After one meeting of may be two to three hours, we were able to conclude the machine order, the technological details and the pricing. As decided mutually, Extrude Hone India was supposed to do the tooling while Extrude Hone Germany did the machine.
We are quite enthusiastic about the overall results, which we have got so far. Extrude Hone gave us good technical support, achieved a timely delivery of the machine. There was a specific deadline requiring the machine to be dispatched by 31st of March. 31st of March the machine left Extrude Hone Germany, which reflects a strong commitment towards customer demands. That goes a long way.
Considering the long history with ZF, the many equipment Extrude Hone delivered for their state-of-the-art automatic gearboxes, processing sun wheel, gear shafts, planetary gears, ring gears to name a few, and our recent support in their latest hybrid projects, the global presence of Extrude Hone, we were confident Extrude Hone would be a supplier of choice.
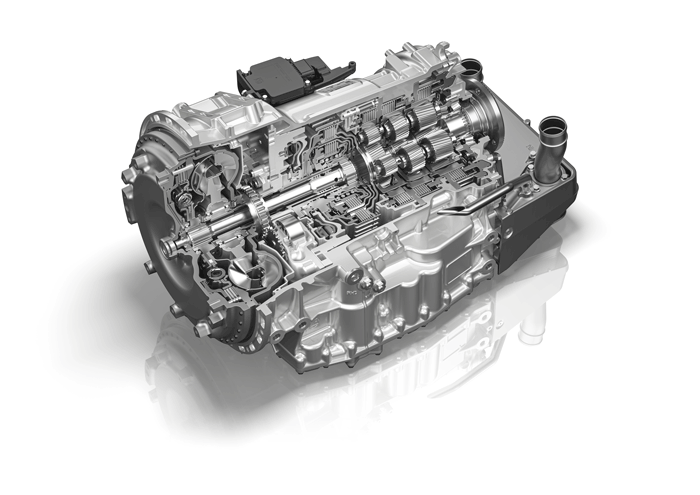
Since, tooling was produced at Extrude Hone India & therefore, trials were conducted at Extrude Hone India. We sent some sample parts as well. Of course, there were some minor issues, which were addressed promptly. Overall things went really well.
The rest is history & we are having a full- fledged ECM deburring process installed & commissioning at our manufacturing plant in India.
Of course, we have yet not started the mass production of the product. Therefore, we have not been able to use your Electrochemical Deburring system on a regular level, but yes, whatever the prototype parts, and pre-series production parts we have produced so far, we are quite happy. And we do hope, that this process should give us good results in the long run.
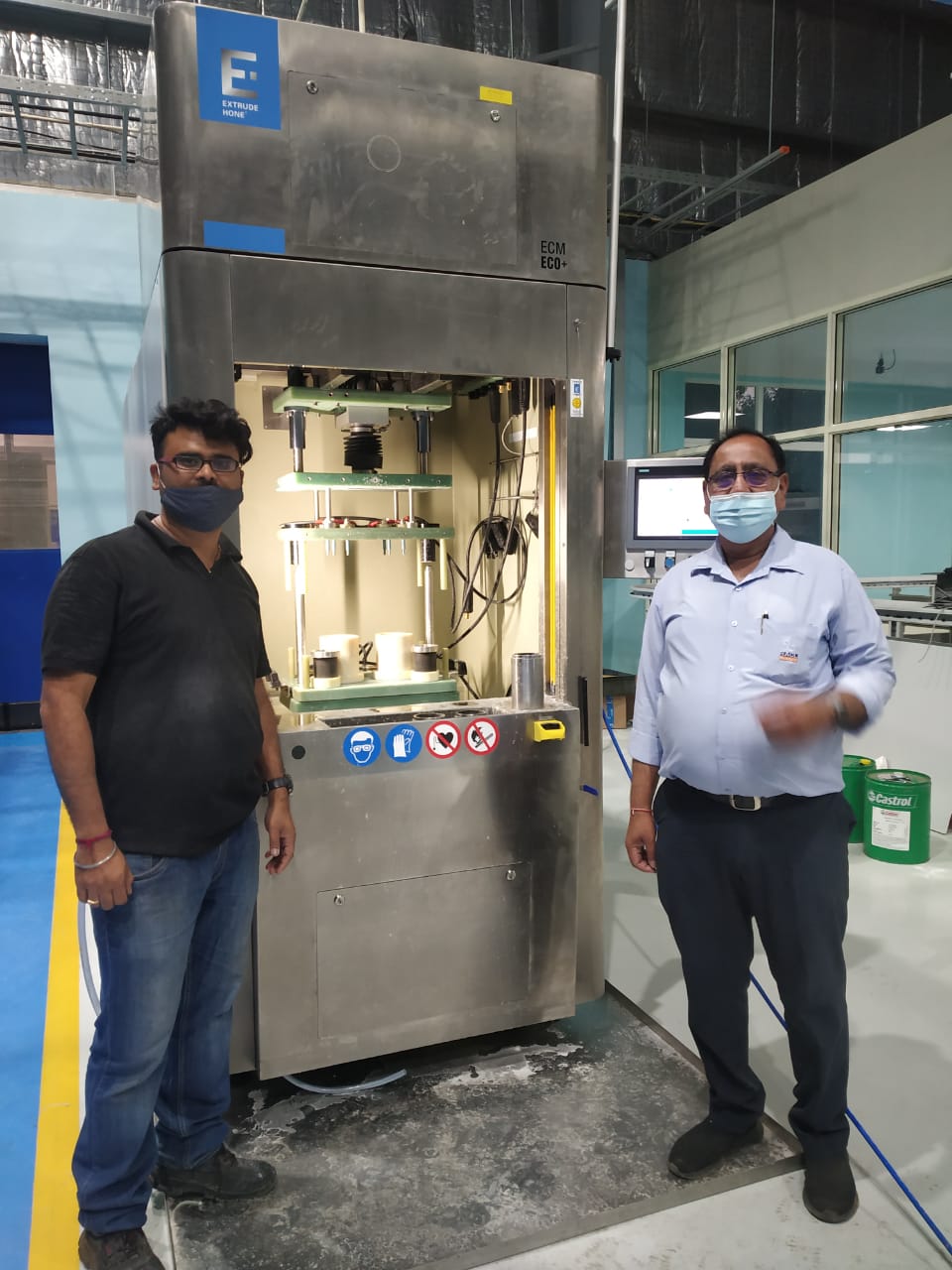
Impressive enough, it was first time we were doing business with Extrude Hone India & Extrude Germany. In fact, we never knew before of Extrude Hone as an Electrochemical Machining process supplier.
Now not to hide anything, while I visited Extrude Hone Germany, I also visited one more company in Germany who offers similar Electrochemical Deburring systems. The basic deciding factor, which went in favor of Extrude Hone Vs other German supplier, was that Extrude Hone has a very big presence in India.
Indian team has a strong technical knowledge as Extrude Hone India is doing a lot of contract shop work. That went into favor of ordering the equipment from Extrude Hone Germany and tooling from Extrude Hone India.
As a global company, it is a very important aspect that we benefit from a complete support in India and the entire tooling manufacturing is taking place in India. You know, tooling is such a thing, that it needs very frequent adjustments or changes or modifications. While we are sitting in India, Extrude Hone is just two hours away, by flight, it becomes much easier & convenient to get support.
In a process like Electrochemical Machining, there’s always the need for frequent technical support, and the need of consistent supply of consumable supply like cathodes or other change over parts. It’s a good initiative taken by Extrude Hone to have a facility in India. This goes without saying.
Our company is a very, very aggressive company in terms of growth. For the last three years, we are growing 20% year over year, except last year when we were almost stagnant because of this COVID situation. We are quite hopeful to continue our growth trajectory again, on the same trends like our past performance, for which we have definite plans. We have very, very aggressive strategy to go into futuristic technologies & product. We are geared up to have our significant presence for EV platforms as well.
Extrude Hone India:
Extrude Hone India is in Bangalore; it is an engineering base supporting the overall Extrude Hone business, a sales and service base, and a contract shop facility which offers access to the three Extrude Hone technologies which are: AFM, ECM and TEM.
The local team provides support to customers across India from the design stage, through feasibility, prototype production and commissioning and aftermarket support for equipment in India. Extrude Hone locally designs and produces tooling for the different technologies.
They are knowledgeable and close to you.
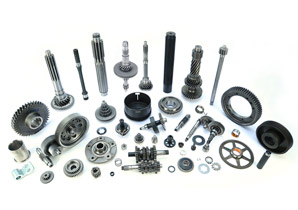
To conclude, the challenge of deburring in gear making has always to remain, and, rather, it has to become more & more stringent in future, as burrs are a major cause of Noise in transmission & future of mobility has a big task of control over NVH norms. Therefore, we eventually foresee a very big cooperation with Extrude Hone.
It becomes more relevant, as at times, the area to be deburred is hard to reach. Same was the case of our component, where we successfully deployed ECM process. We are quite happy, at first it is very fast, and it really reproduces within narrow tolerances. Other deburring processes do not work in so narrow tolerances, as compared to ECM. Our first attempt to deploy ECM technology has given us many insights into this technology, and definitely we may use this process for future projects as well. And yes, now I can say that even though, it is an expensive process, it solved our problem & the results are here.
We also conducted a Thermal Deburring trial for some of our components, but we were not successful, because burrs were too big. I’ve seen Abrasive Flow Machining as well when I visited Extrude Hone Germany, so I have a fair idea of all the three technologies. We will consider these technologies as well,
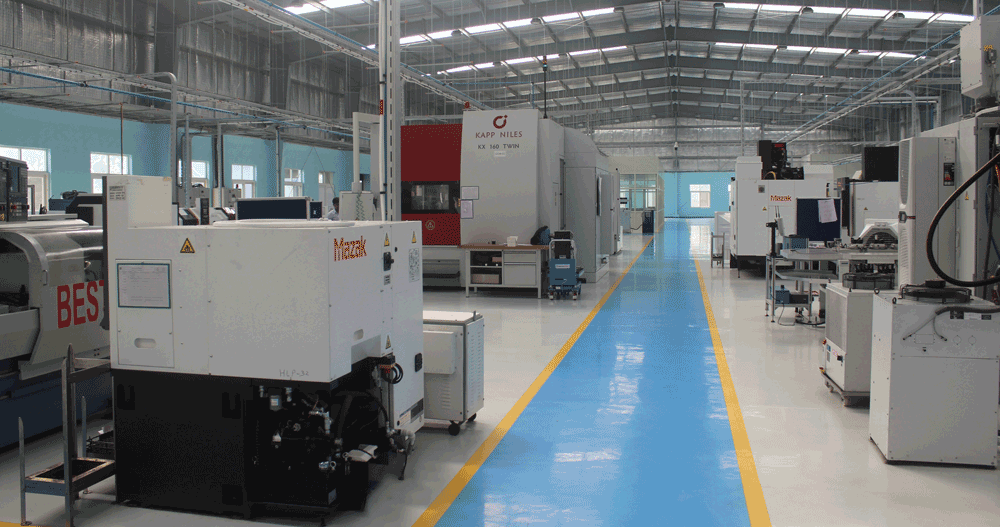
wherever the need may arise in future. In fact, right now, we are discussing with Extrude Hone India for a new RFQ from a USA customer. As we are quoting project to the Customer, we have made a strategic decision to offer ECM process in our offer itself.
Specifically, regarding our company, we are a company producing gearing solutions to niche markets and premium segments. The opposite of the mainstream in India, where there is a mass market for 2-wheeler. Our USP is that we are a fully integrated company, which is having all the solutions under one roof. Looking at gear manufacturing, we have all kinds of technologies required within our own company, and we really provide solutions to our customers for complex parts. We work with our customers with a concept called ‘concurrent engineering’, where we involve ourselves with these customers, right from the initial concept sheet or the initial design stage, so that we work hand in hand with the customer to provide them solutions via a manufacturable product on a low-cost basis and with value engineering support.
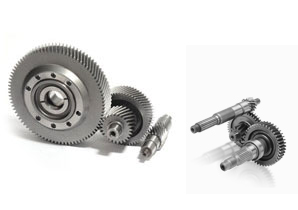