
ABRASIVE FLOW MACHINING (AFM) ENHANCES PUMP EFFICIENCY
In modern world, energy efficiency is the key to sustainable living. And efficiency of pumps matters significantly because they consume almost a quarter of world’s energy consumed by electric motors.
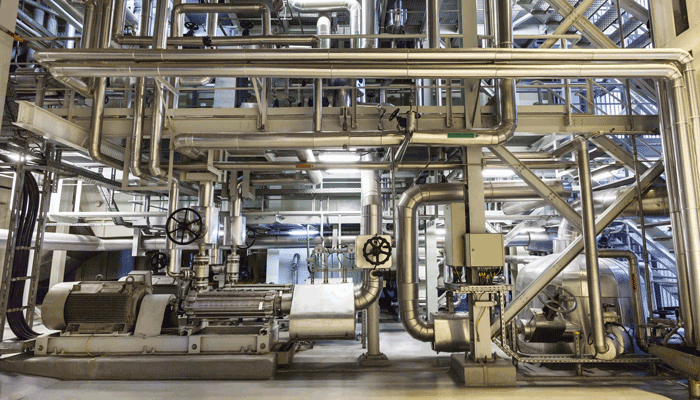
Over past several years, the end users have pushed the industry and researchers to concentrate on pump efficiency to save energy. However, when pump efficiency reaches a relatively high figure, it becomes much difficult to do further optimization. And at this stage, surface roughness of pump components plays more and more important role in improving pump efficiency.
Computational Fluid Dynamics analysis indicates:
- Surface roughness of the flow passage has significant influence on pump performance
- And its effect is more on pump efficiency than head
- The influence of surface roughness is more significant on hydraulic and mechanical efficiencies than volumetric efficiency
- The hydraulic efficiency is affected mainly by the surface roughness of impeller and diffuser
- With increased flow rate and rotational speed, surface roughness has more significant, inhibiting effect of efficiency
So, in a nutshell, improvement in surface roughness of impeller and diffuser of a pump with large flow capacity and high operating speed can improve its efficiency.
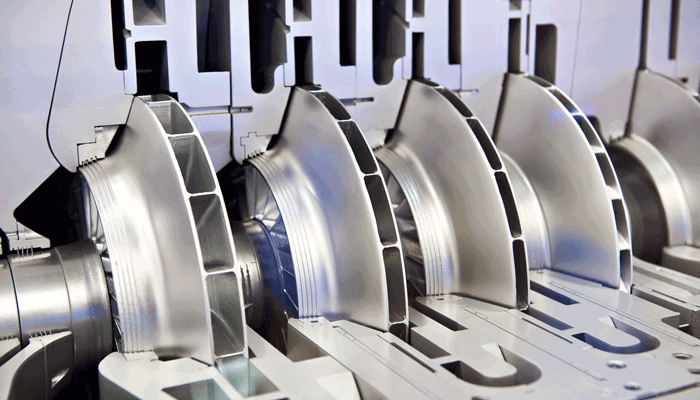
Impellers and diffusers, whether cast or 3D printed, have inherent surface imperfections. Even with the best of available processes, they can hardly match the need of their customers. With complex, narrow internal passages, conventional finishing processes reach their limits, soon.

In order to deliver a consistent polished surface, AFM is used as a repeatable process. AFM uses abrasive laden high viscous paste, called media, which is pressurized thru’ flow passages in a controlled manner. Media like any fluid, flows thru’ the passages, polishing the surfaces, working the most in areas where resistance to flow is the highest.
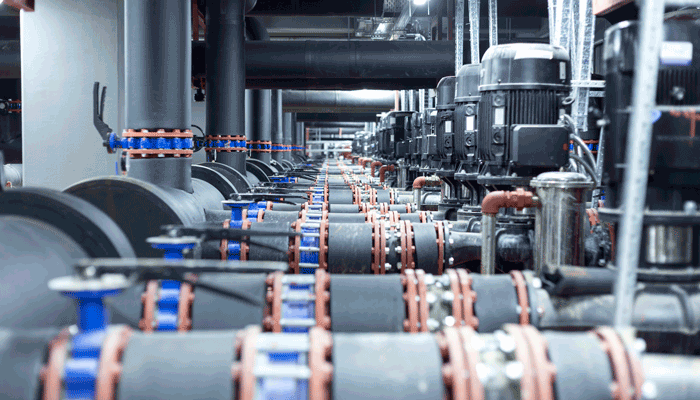
AFM improves surface roughness in flow passages of impeller and diffuser drastically, sometime up to 10 times, improving pump efficiency from 1% to 11% depending on the type, design and initial condition of the components.
Extrude Hone has decades of expertise in working together with OEMs, foundries, 3D printers, re-conditioners and end users in delivering best of efficiencies in some of the most demanding applications. From power generation to mining and even space applications are benefitted by Extrude Hone’s AFM process expertise.
Similar gains can be expected in all fluid machines. Apart from pumps, turbines and compressors have gained significant advantages from Extrude Hone’s AFM process. From aero impellers, guide vanes, blades and swirlers, to pump impellers and guide vanes, industry leaders have trusted Extrude Hone’s AFM process for decades.